The purpose of this article is to address many of the common questions and concerns regarding the software set-up process for InspectNTrack Smart Safety’s lockout tagout software.
We are seeing a trend in the industry, with more and more companies looking for software solutions to integrate into their operations. Unfortunately, sometimes these decisions are made too hastily, leaving safety professionals stuck with software that has major drawbacks despite being intended to easily facilitate inspection and maintenance management on safety assets.
Common issues we hear about include surprise billing and escalating expenses due to pay-per-scan or pay-per-customer setup pricing models. Other times, the software package lacks the features needed to accomplish lockout tagout on a range of machinery. Whatever the reason, a better lockout tagout platform, such as InspectNTrack Smart Safety, is available to replace those issues with newfound efficiency.
So whether you’re looking at InspectNTrack Smart Safety LOTO as a potential first-time software or as a replacement for one that isn’t working well, this article should help you walk away with a better understanding of what exactly our software offers and what you could expect during integration.
Don’t worry if you have questions like
- “How will I get my data out of the old system and into InspectNTrack Smart Safety’s platform?”
- “How do I get the software configured to my specific requirements?”
- “How will I learn to use something new?”
- “How long will the software conversion process take?”
You can feel comforted knowing that our implementation team has answers to these questions and more. Our goal is to make the software conversion process as painless as possible so that your team can migrate to the new software program with as little disruption as possible. So, let’s dive into the information!
Why Should We Transition to Smart Safety Lockout Tagout Software?
Why implement our LOTO software? Because it will revolutionize your lockout tagout program and operations.
Organizations often hesitate to adopt new software because of perceived costs, complexity, or disruption. However, our lockout tagout software offers several features and benefits that can totally transform loto processes in the workplace.
Features that Set InspectNTrack Smart Safety Apart:
- Customizable procedure building
- Paper-free documentation
- Detailed audit history
- Wifi is not required for use
- A centralized location for information and reports
- QR code scanning for quick access to procedure steps
Top Advantages to Using Our Software:
- Organized Records
- All your data in one place.
- On-the-Go Reporting
- Save time by filling out reports while the job is being completed.
- Automated Action Triggers
- Never miss an audit, repair, procedure, etc.
- Increased Efficiency
- Perform lockout tagout quicker and easier than ever before.
- Greater Accuracy
- Reduce human error in documentation with steps for completing reports, notifications, and a digital trail of information.
- Improved Transparency
- Detailed reports allow management to check in on operations and ensure that everything is up to standard.
- Simplified Compliance
- Cost Savings
- Workers who can perform maintenance more quickly can devote their time to other company operations.
- Scalability
- Our software easily adapts as your organization grows or changes equipment.
These software features and benefits help managers create a lockout tagout program that is efficient, compliant, and intuitive for workers. To learn more about how Smart Safety software could aid you in performing lockout tagout, request a demo!
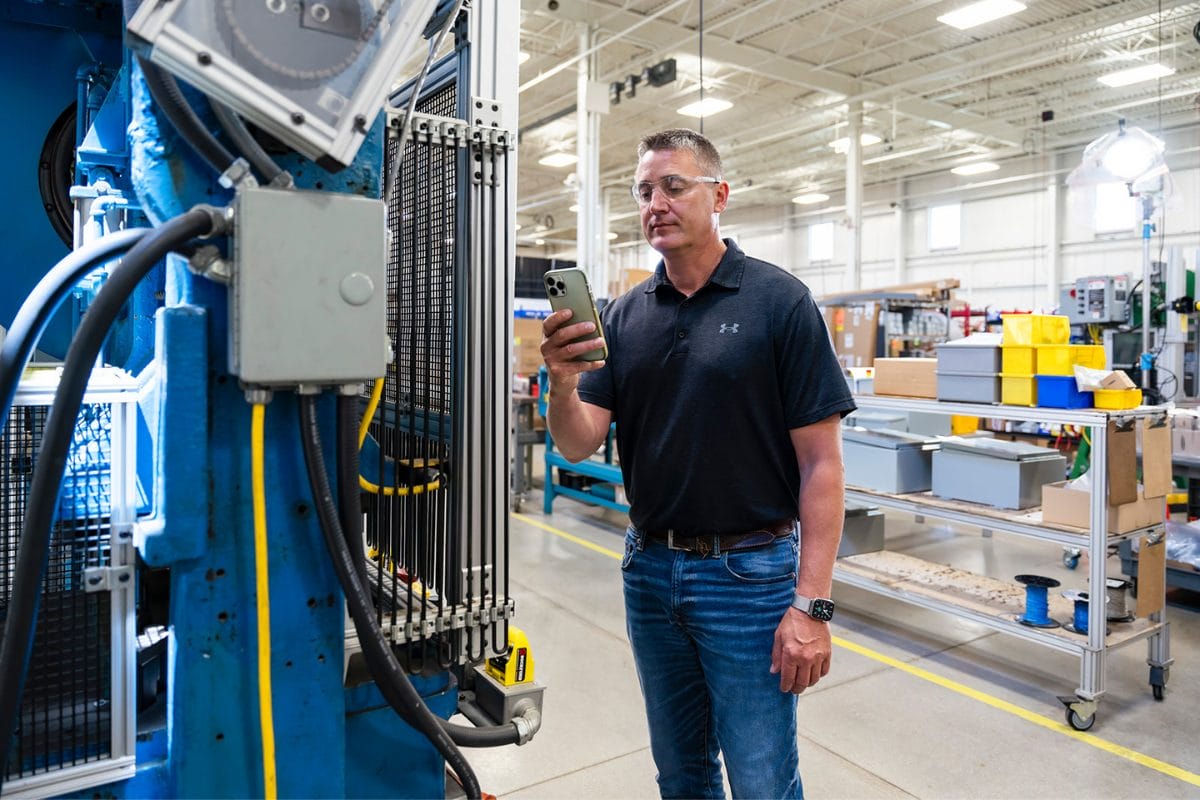
What Does the Software Set-Up Process Look Like?
The transition to implement lockout tagout software typically follows these steps:
Step #1: Meet with Your Implementation Specialist
Every new InspectNTrack Smart Safety client is assigned an implementation specialist. The implementation specialist directs the software set-up process and personally works with the client until the system is set up and live. The implementation specialist is your key to a smooth transition, ensuring that each step is done properly and on schedule.
Step #2: System Customization and Configuration
Next, the implementation specialist will work with company leaders to determine what controls they want set up in the system. Then, accounts will be made for admins and other users, with other information added such as the various forms of machinery and site map setup. This step in the process will allow the company to dictate their needs and have the software customized to best work within the organization’s parameters.
Step #3: Employee Training
The next phase of the software set-up process is training employees to utilize the software in their operations. Companies have the option to receive remote or in-person training from their implementation specialist, which provides a flexible approach to educating employees on using the software effectively. No matter which option is selected, the implementation specialist will then provide in-depth training on software features and how to use them, with role-specific training for administrators, authorized workers, and affected employees.
Step #4: Go-Live & Support
After employees have been trained, they can be given access to the software and begin using it to create lockout tagout procedures and perform LOTO. As with any change, there will be adjustments needed, but the InspectNTrack Smart Safety team is always ready to help. Newcomers can feel confident that ongoing support from our team will help make the set-up process and software integration as seamless as possible.
How Long Will The Software Set-up Process Take?
The timeline for set-up depends on factors such as company size and the desired complexity of set-up functions. In general:
- Small organizations may complete the set-up process in a matter of a few days or weeks.
- Larger organizations with complex operations and many facilities may require several weeks or even months. This is because there will be a lot of accounts to make, employees to train, and machinery to input.
Regardless of company size, your assigned implementation specialist will ensure that your software is configured to your specific needs.
One thing that sets InspectNTrack Smart Safety apart from other software platforms is its configurability. Our software comes with many options for adding machinery, creating custom lockout tagout procedures, information access controls, and more. Factors such as the set-up of these controls, the number of employees impacted by the software integration, volume of lockout tagout machinery/equipment, and the number of facilities will all impact the length of the software set-up process.
Will This Disrupt Our Current Operations?
There should be very minimal disruption to operations during the software set-up process.
While some level of disruption is inevitable during any transition, workers will be able to operate as normal up until the new software is live and ready for use. Two different programs can be run simultaneously until go-live. This makes it possible for management and workers to still access and use any of the former systems and data while the set-up is completed.
The main disruptions to operations will come in the form of
- Employees receiving a scheduled training
- Workers adjusting to a new way of performing and documenting lockout tagout procedures in the Smart Safety software
Good communication and step-by-step integration will help ensure that the transition is seamless and that there are no compromises on safety or productivity.
What About Using QR Codes?
Although not required, Smart Safety software works best when used with QR codes. These codes can be used to connect pieces of machinery and equipment that require lockout tagout with their equipment-specific lockout tagout procedures. That way, a worker can use the software to easily scan the QR code on machinery and have it pull up the associated procedures and reporting in an instant.
Now, let’s talk about the role that this feature plays in the software set-up process. Depending on your current operations, you’ll likely find yourself asking one of these two questions:
What if we already have QR codes on our machines? If your machines are tagged with asset tags such as barcodes or QR codes, the asset ID numbers associated to each machine can be uploaded into the equipment record. This offers the ability to scan the machine asset tag rather than a procedure to launch a LOTO, annual audit, or issue.
How do I get LOTO procedure specific QR codes. Our software allows for LOTO procedures to be developed within minutes. Upon submitting a finished procedure, a unique QR code will be system generated to identify the procedure. This system generated QR code prints at the top of the procedure report that is attached these to each machine, making it possible for a worker to simply scan the code to auto-launch a digital lockout or return to service.
Regardless of whether or not QR codes are already integrated into your process, InspectNTrack Smart Safety software can handle them easily during software set-up.
How Will I Get Employees Adapt to the Change?
Some of the best ways to encourage widespread adoption of the new software include providing employees with sufficient training, highlighting the benefits to using it, inviting feedback, and sharing expressed support from leadership. Resistance to change is natural, but it can be mitigated by addressing employee concerns and involving them in the process.
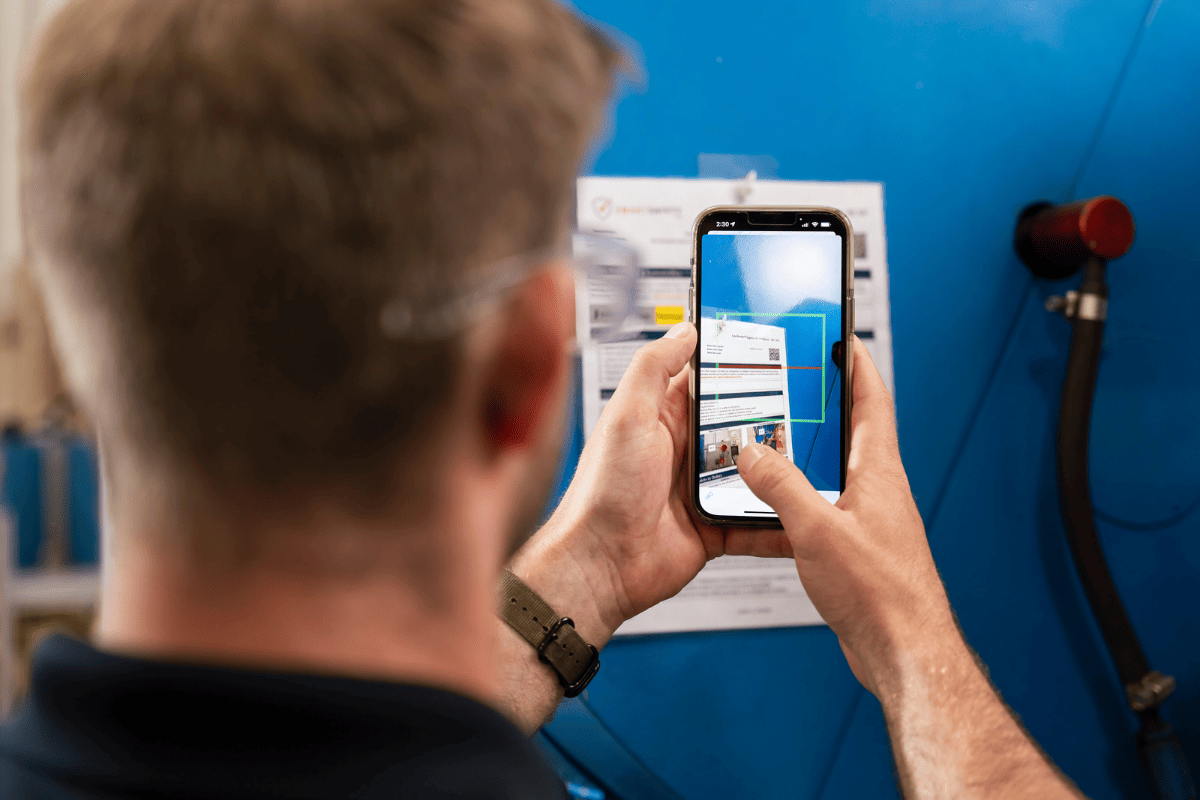
Is the Software Secure and Reliable?
Data security is a common concern when adopting new software. InspectNTrack Smart Safety has taken strides to ensure that our software solution is a secure form of data storage, both during the software set-up process and after.
Here are some factors that can bring peace of mind.
- Secure Data Storage: Our software is a SaaS solution that uses cloud storage to safely store all compliance records, procedures, and audit logs that are stored in the secure database.
- Backup and Recovery: Routine backups serve as protection against any data loss and are part of a thorough data protection strategy.
- Reliable Support: Should there ever be an issue, the Smart Safety team is always ready to act, with a strong customer support team that is dedicated to maintaining reliability and security.
InspectNTrack Smart Safety understands how critical data security is and is committed to making it a priority for all clients.
How Do We Ensure Compliance During the Conversion Process?
Compliance with OSHA and ANSI regulations is non-negotiable, even when transitioning to a new software. Thankfully, this is easy to do with InspectNTrack Smart Safety.
Here are some steps that can be taken to ensure compliance during the software set-up process:
- Continue Performing LOTO as Usual – As mentioned earlier, the company can continue with its previous way of performing lockout tagout until the software is fully set up and ready for use, whether that be in a different software or manually.
- Maintain Proper Documentation: Any procedures or other maintenance efforts made while the software is set up still need to be properly reported and documented. Ensure that employees understand this. Additionally, consider having duplicate records if transitioning from another software, to verify that no information is lost in the transition.
- Audit Procedures Early: As news procedures are created in the Smart Safety software, workers should review the procedures and check that they meet regulatory standards.
- Communicate Effectively: Word of upcoming changes may leave workers feeling confused about what work is and isn’t ok to continue doing. Management must take responsibility to inform workers about the change but also set expectations for efforts during the transition phase.
What Are the Costs and ROI?
Costs for investing in lockout tagout software vary depending on features and organizational size. Organizations are encouraged to sign up for a brief demo with one of our team members. This offers an opportunity for our team to help answer any questions and get a feel for what all your organization is in need of.
InspectNTrack Smart Safety is committed to providing a fair price. We want our clients to feel that the investment is well worth it. And many do! They recognize the ROI and continue with our services.
So what results can clients expect, in terms of ROI? Here are a few:
- Our 90% faster mobile app leads to fewer hours needed to accomplish the same work, which lowers production costs.
- Avoided lockout tagout injuries result in avoided hospital bills, legal battles, reputational damage, and worker’s comp.
- Better care for machinery translates into fewer replacements and a longer life span for equipment.
- Tighter compliance efforts drastically reduce the likelihood of costly OSHA fines for violations of regulations.
How Can We Ensure Long-Term Success?
After implementation, maintaining and optimizing the software is critical. Some strategies for ensuring long-term success include:
- Regular Updates: Keep the software up-to-date with the latest machinery and lockout tagout procedures that are in use. This will help ensure compliance.
- Ongoing Training: Refresh training periodically to ensure employees stay proficient at using software to perform lockout tagout and document their efforts.
- Continuous Feedback: Collect employee feedback to refine procedures and maximize software utility.
- Gaining Insights and Making Improvements: Use the software to gain insights about high risk areas, quality of work from different employees, and more. Utilize this information to make improvements.
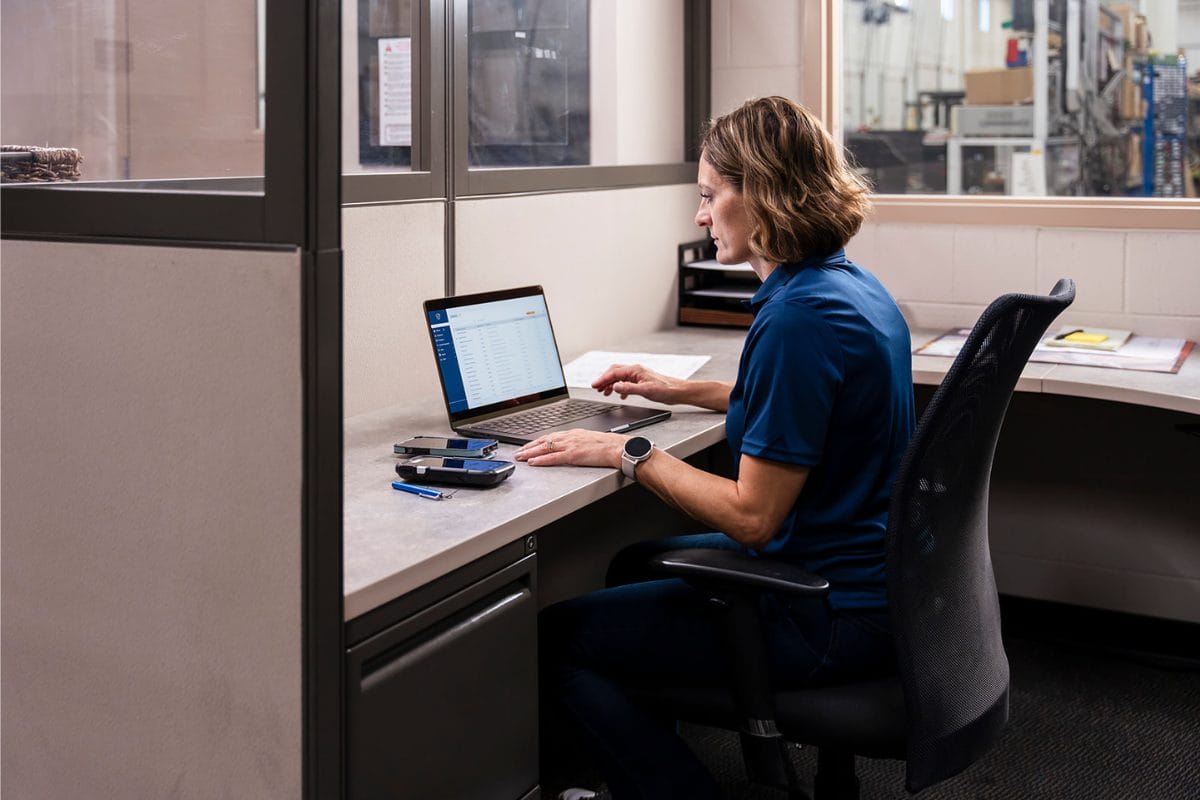
Conclusion
While investing in a new software solution can seem risky, InspectNTrack Smart Safety is here to answer all questions and concerns. This article dives into the details of the software set-up process such as how long the transition takes, how it will impact current operations, and how to ensure compliance during the change. After all, setting up and integrating lockout tagout software is a worthwhile investment that enhances safety, compliance, and operational efficiency. This article helps put worries at ease by laying out the steps for implementation. At Smart Safety, we plan to make the software set-up process smooth and successful by addressing common concerns, planning carefully, utilizing the implementation specialist and leveraging the software’s capabilities. With the right approach, implementing LOTO software becomes a key step toward a safer and more streamlined workplace.
Our goal is to make the software conversion process as painless as possible so that your team can easily adjust to the new software program.
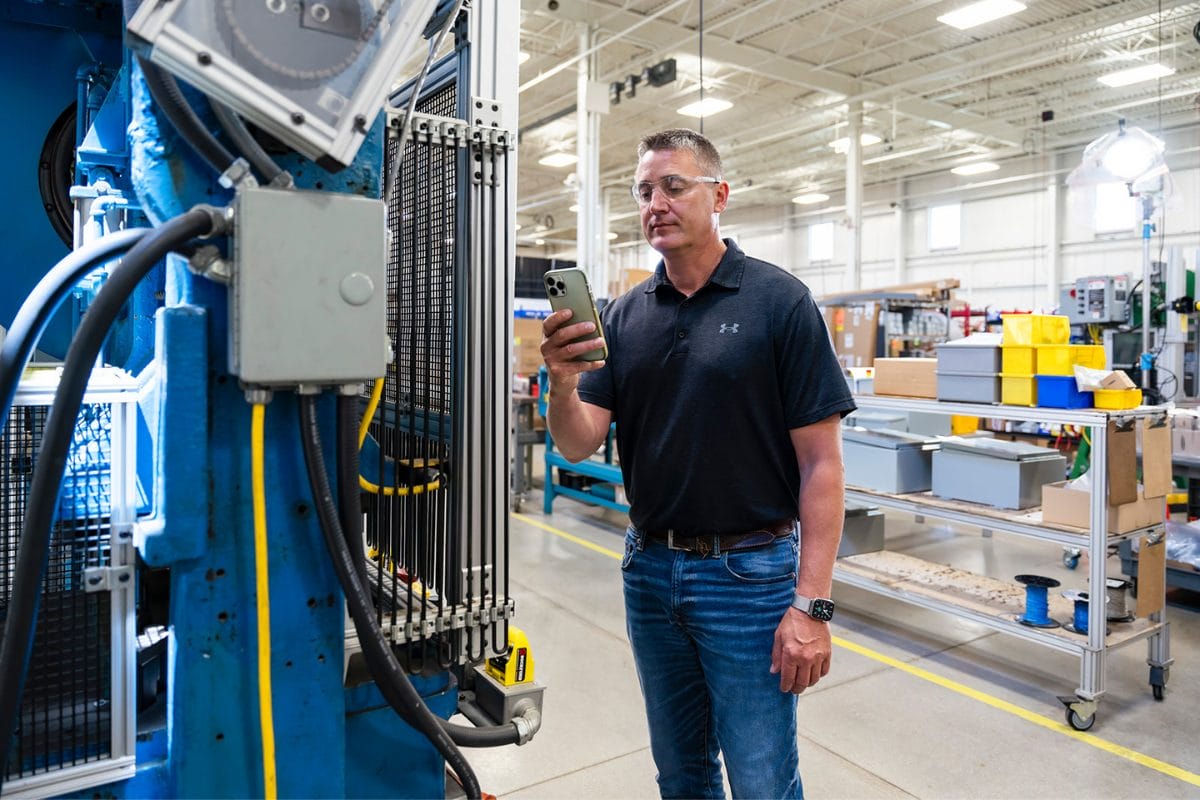