Simplify and modernize your lockout tagout program with digital lockout tagout. This article explains what digital loto is and how it can make your job easier.
We all know lockout tagout. It is the process used to ensure safety of workers when dealing with hazardous energy sources, such as those found on large machinery or manufacturing equipment. We also know how tedious it can be to try and keep up with periodic inspections schedules or to keep reports organized, especially for upcoming audits.
That is why InspectnTrack Smart Safety has designed a user-focused solution: software that enables digital lockout tagout.
In this article we will dive into the specifics of digital lockout tagout and give you a clear vision for how it can support your lockout tagout program. We will expand on topics such as what it is, the benefits of using technology for loto procedures, and how it actually works.
What is Digital Lockout Tagout?
Digital lockout tagout is the process of performing lockout tagout procedures while simultaneously recording the act in a digital format such as on a phone, tablet, handheld scanner, or computer. The term can also be more loosely used to refer to incorporating technology into other LOTO related actions such as writing procedures, storing reports, or scheduling future tasks.
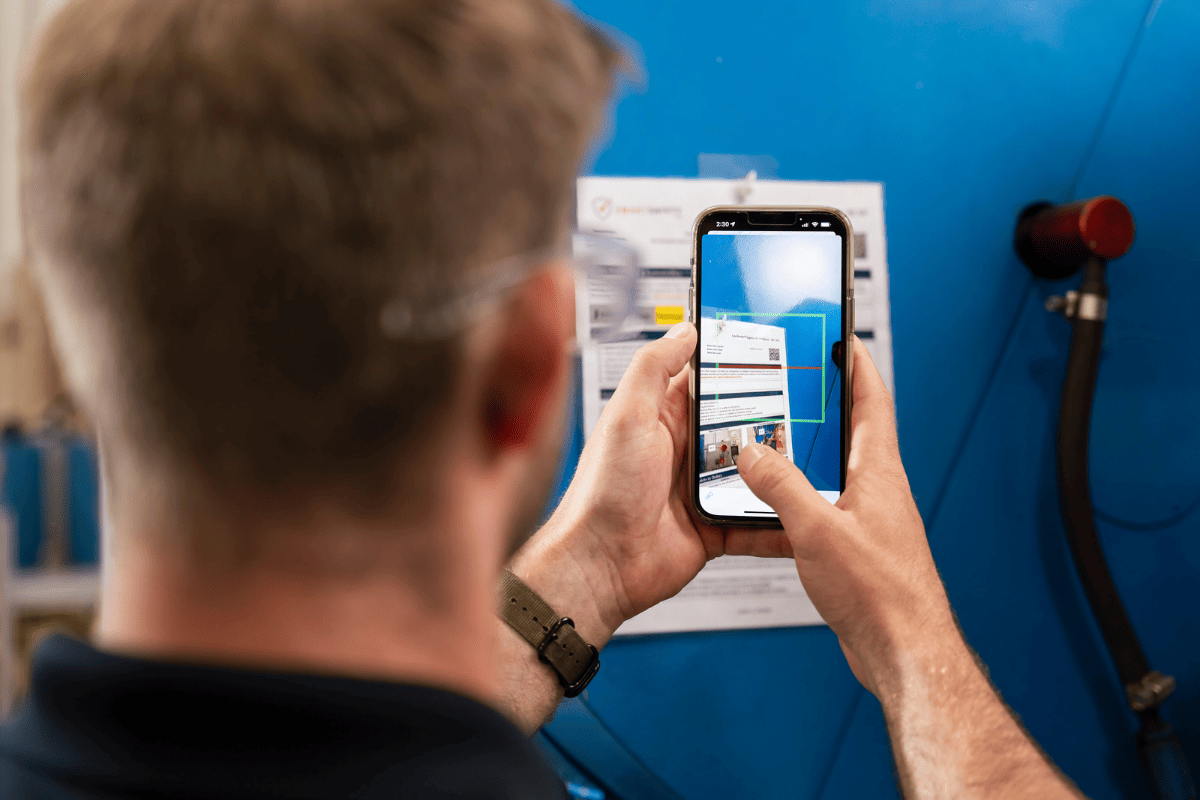
Digital vs. Traditional Lockout Tagout
Digital lockout tagout differs from traditional methods in that it shifts away from relying on paper-based processes to document and manage loto efforts.
Traditionally, many organizations have relied on physical papers or small forms of technology (such as Excel spreadsheets or digital calendars) to get the job done. While these options aren’t bad, anyone who has used them understands that this approach can feel dated, slow, and ineffective. Having information spread out across multiple mediums can make your program feel disjointed.
Digital lockout tagout, on the other hand, brings all data and tasks into a central location, making it much easier to access and add to current information. Thanks to software applications like InspectNTrack Smart Safety, digital lockout tagout can be performed with virtually any device and information can be accessed in the platform anytime, anywhere.
Benefits of Performing Digital Lockout Tagout
One of the primary ways lockout tagout software can simplify your operations is by providing a single location for you to perform all functions related to your program, including writing procedures, performing them, scheduling inspections/maintenance, and recording any jobs.
This central location for storing data and managing tasks brings a multitude of benefits including:
How Digital LOTO Simplifies Procedures and Compliance Efforts
Our software is designed to make your job easier. Specifically, it is meant to simplify the creation and usage of equipment-specific lockout tagout procedures, while also helping you maintain compliance with regulations such as OSHA 1910.147 and ANSI Z244.1. Here are some of the intentional design aspects that make that possible.
Mobile Accessibility
InspectNTrack Smart Safety comes in app form, meaning that the software can be used on practically any device that runs on iOS, Windows, or Android. It works with mobile phones, desktop computers, tablets, handheld scanners and more. This means that workers can carry the technology with them on the job site, in their pocket, vest, or hand. Mobile accessibility helps users stay well-informed, which supports compliance and aids in performing procedures.
QR Code Scanning
With InspectNTrack Smart Safety software, authorized users can easily create their own lockout tagout procedures and maintenance checklists. This information is then connected with a QR on the equipment it is meant for. When users scan the equipment’s QR code, the necessary information will immediately come up, making it easy to perform the correct steps on assigned machinery/gadgets. Software and QR codes make a fine team that reduces human error and supports compliance.
On-the-Go Reporting
Something that sets our software apart is the fact that it doesn’t need wifi to function or update. This means that any form of LOTO procedures, periodic inspections, or procedure building can be completed without any data connection. This helps encourage users to fully report on their efforts by removing the hassle of papers and filling out reports manually. Plus, it can be used in hazardous areas, remote areas, and everything in between.
Organized Documentation
When you use our software for digital lockout tagout, all of your program data is brought together in a centralized data platform. This helps to keep data organized and easily retrievable in the event of an audit. Within seconds, reports can be pulled up, shared, or printed. You never have to worry about lost paperwork or missed compliance tasks.
Dynamic Scheduling
InspectNTrack software can be used to stay up to date on both upcoming lockout tagout procedures and required maintenance. The system automatically schedules upcoming inspections for equipment and systems to ensure that they are routinely completed. Inspections can be grouped together based on area, timing, or shifts and assigned to a single person or a team of technicians. This feature helps remove the pain of managing various LOTO schedules for different kinds of equipment, making compliance that much easier.
Action Triggers and Alerts
If there are any reported issues during lockout tagout procedures, the system will notify users of the issue. These notifications encourage a prompt response from company personnel to perform the needed actions and promote safety. Workers and managers alike can see what tasks need to be done and coordinate together to make sure they are completed.
Steps to Completing Digital Lockout Tagout
Step 1: Scan and Start
To begin a digital lockout tagout procedure, start by navigating to the procedure steps. This can be done either by scanning the QR code for that piece of machinery or looking up the procedure in the app. (Each machine or piece of equipment generally has a laminated version of its lockout tagout procedures attached to the side with a unique system-generated QR code printed at the top.)
Step 2: Follow the Instructions on the Lockout Tagout Procedure
After the application steps are displayed and completed, the first step of the procedure is displayed on the screen. It includes the energy source and its location, the image, isolation instructions, and verification instructions. Slide the completion button to confirm that the step was completed. The next step is then displayed.
Step 3: Finalize Reporting
As you go through the lockout tagout steps, you will be filling out information about the procedure. However, there may be additional info that you need to add at the end. It’s a best practice to look back over the information and make any final notes before finishing the report. Of course, you can always go back in later to make adjustments if needed. It is just easier to do it in the moment if possible.
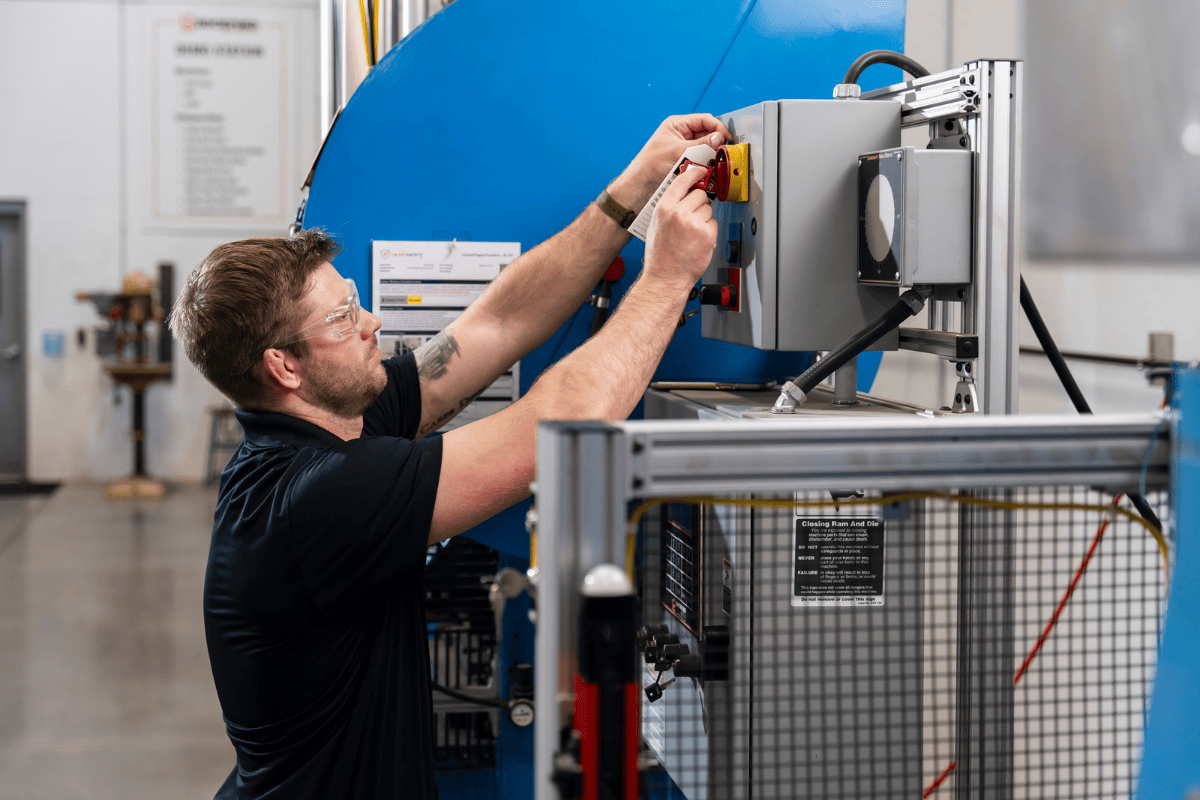
Choose InspectNTrack Smart Safety Software
As time goes on, more and more companies are making the switch and integrating software capabilities into their lockout tagout programs. With benefits such as paperless documentation and real-time updates, integrating digital lockout tagout with software is a no-brainer for a lot of organizations. However, it makes sense to be hesitant or want to learn what you can before diving in.
At Smart Safety Pro, we don’t want you to just choose our software, but we want you to love your choice. To help you decide whether or not our program works for your situation, we offer free demos.
With a free demo, you can set up a time to meet with one of our professionals and talk about your organizational needs. This way, you can gather information and make an informed decision about what’s right for your company’s future.
Click here to learn more about how Smart Safety Pro can enhance your lockout tagout program.
Conclusion
Thanks to software solutions, digital lockout tagout is the future of lockout tagout. Digital lockout tagout is the process of performing lockout tagout procedures while simultaneously recording the act on a mobile device. It differs from traditional methods by using technological advancements to shift away from ineffective practices. Not only that, but digital lockout tagout helps to streamline operations, improve efficiency, and enhance team collaborations.
Software makes your job easier by automating scheduling, providing real-time updates, organizing data into a single location, and so much more. InspectNTrack Smart Safety offers software that is designed to simplify running a lockout tagout program and maintaining compliance. It is easy to integrate into the normal lockout tagout process and made with the customer in mind.
Want to learn more about our lockout tagout software? Request a free demo! Start exploring digital lockout tagout solutions today so you can future-proof your workplace and be ready for whatever comes tomorrow.
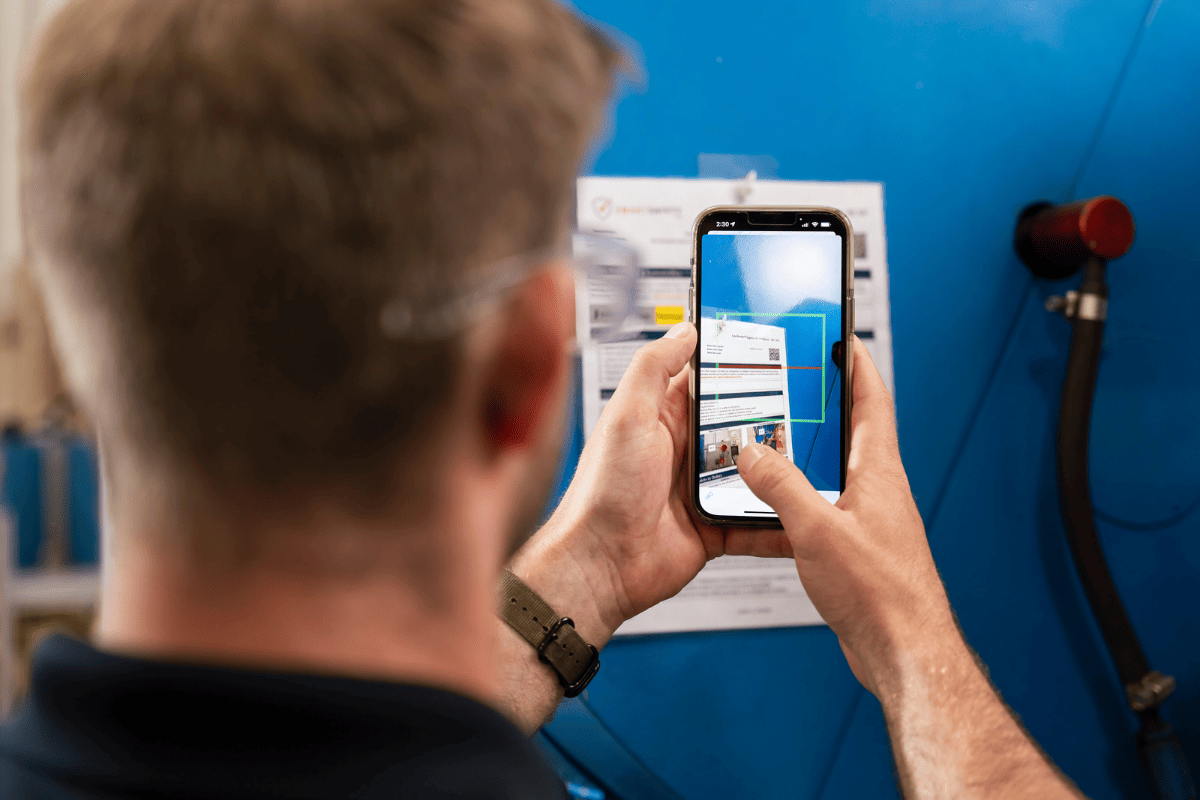