In the food manufacturing industry, the safety of workers is paramount, particularly when it comes to maintaining and servicing equipment that handles various stages of food processing. One of the most effective safety protocols to prevent accidents and injuries is the implementation of Lockout Tagout (LOTO) procedures. LOTO is designed to control hazardous energy sources and ensure that machinery is properly shut down and isolated before maintenance work begins. This article explores the importance of lockout tagout in the food manufacturing industry, its specific challenges, and best practices for implementation.
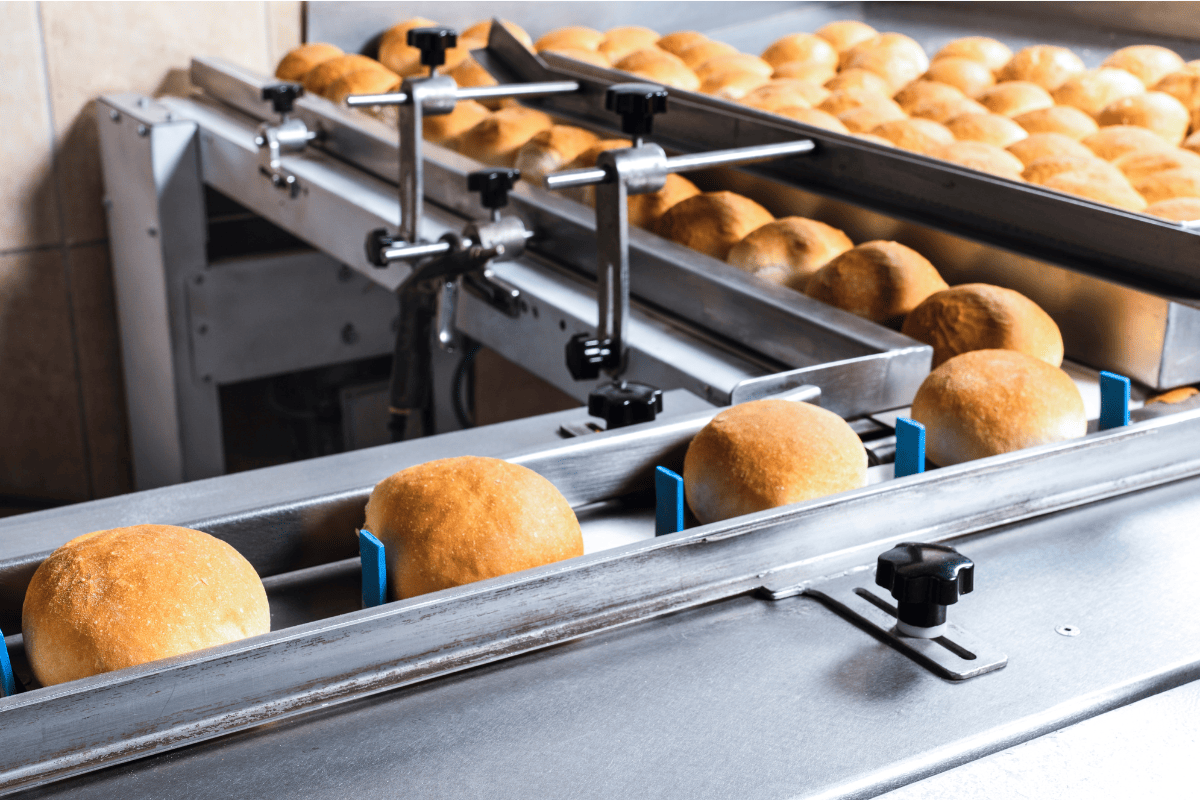
Why Lockout Tagout Is Important for Safety in The Food Processing Industry
Food processing and manufacturing often relies on industrial equipment and machinery to complete operations. However, sometimes this machinery needs maintenance or servicing to ensure that it functions properly. Lockout tagout is a safety measure that can and should be used during maintenance/servicing activities on any equipment that involves hazardous energy, including equipment used in the food manufacturing industry. Implementation of LOTO procedures during repairs or work on machinery can help maintain safety for workers and product consumers.
3 Primary Purposes of LOTO in The Food Industry
While there are many functions and benefits of performing lockout tagout procedures in food manufacturing and processing, here are 3 primary purposes:
Purpose #1: Preventing Accidents and Injuries:
- Explanation: The food manufacturing industry involves complex machinery such as mixers, conveyors, grinders, and packaging equipment. These machines can pose significant risks if not properly de-energized before maintenance. Lockout tagout procedures help address these safety hazards by minimizing their opportunity for harm and providing a controlled environment for maintenance.
- Relevance: LOTO procedures are essential to prevent accidental start-ups, which could result in severe injuries, such as amputations, lacerations, or even fatalities. Proper implementation of LOTO protects workers by ensuring that all energy sources are isolated and controlled.
Purpose #2: Maintaining Food Safety Standards:
- Explanation: In addition to protecting workers, lockout tagout helps reduce the risk of injuries that could lead to product contamination. This encourages food safety and the production of top-tier products.
- Relevance: Uncontrolled energy or improper shutdown of equipment can lead to the release of contaminants into the production process, compromising food safety. By ensuring that machines are safely and securely shut down, LOTO helps maintain the integrity of food products.
Purpose #3: Compliance with Regulations:
- Explanation: The food manufacturing industry is highly regulated, with strict standards for worker safety and food quality. Lockout tagout provides a way for companies to safely check the conditions of their equipment, make necessary repairs, and ensure compliance with established regulations.
- Relevance: Implementing LOTO is not only a safety measure but also a regulatory requirement. Compliance with OSHA standards and other industry-specific regulations is critical to avoid penalties, legal liabilities, and reputational damage.
Regulations to Know for Lockout Tagout and Food
In the food manufacturing industry, compliance with safety regulations is not just a legal obligation but also a critical factor in protecting workers and ensuring the safety of food products.
Lockout Tagout (LOTO) procedures play a central role in these efforts, as they prevent the accidental release of hazardous energy during maintenance and servicing of equipment. This section outlines the key regulations that govern LOTO and food manufacturing safety, emphasizing the importance of understanding and adhering to these standards.
Compliance with LOTO regulations is a critical component of safety management in the food manufacturing industry. By understanding and adhering to OSHA’s LOTO standard, FDA regulations, ANSI guidelines, and other relevant local and international standards, food manufacturers can create a safe working environment, prevent accidents, and maintain the integrity of their products. Regular training, thorough documentation, and the integration of LOTO procedures into overall safety programs are key strategies for achieving and maintaining compliance.
3 Key Compliance Strategies for Food Manufacturing/Processing
Upkeep for large machinery can be difficult, particularly for corporations with large volumes of sites, equipment pieces, or staff. Here are 3 strategies that companies can employ in order to stay organized and on top of their game.
1. Regular Training and Updates: Though the steps in lockout tagout procedures are often similar, various types of equipment may require different care. This is due to factors such as the specific isolation points, shutdown procedures, and more. Because of this, it is vital for those in the food manufacturing industry to provide thorough, ongoing training to employees about lockout tagout. Additionally, workers should be made aware of any updates to relevant standards or company policy. Training gives staff the tools to successfully and safely complete LOTO procedures.
2. Comprehensive Documentation: Keeping detailed records of LOTO procedures, training sessions, inspections, and audits is crucial for demonstrating compliance during regulatory reviews or audits. Companies should make it a priority to inform workers on how to properly document and file any inspections/reports related to lockout tagout procedures. That way, necessary information and documents can be retrieved when needed.
3. Routine Inspections/Maintenance/Testing: Creating and following an inspection schedule is a profound way to maintain compliance. By using a schedule, managers can see upcoming inspections, make assignments, and plan for necessary jobs. Since many regulations have guidelines for the frequency and depth of inspections, a schedule can increase the likelihood that all tasks needed for compliance are accomplished.
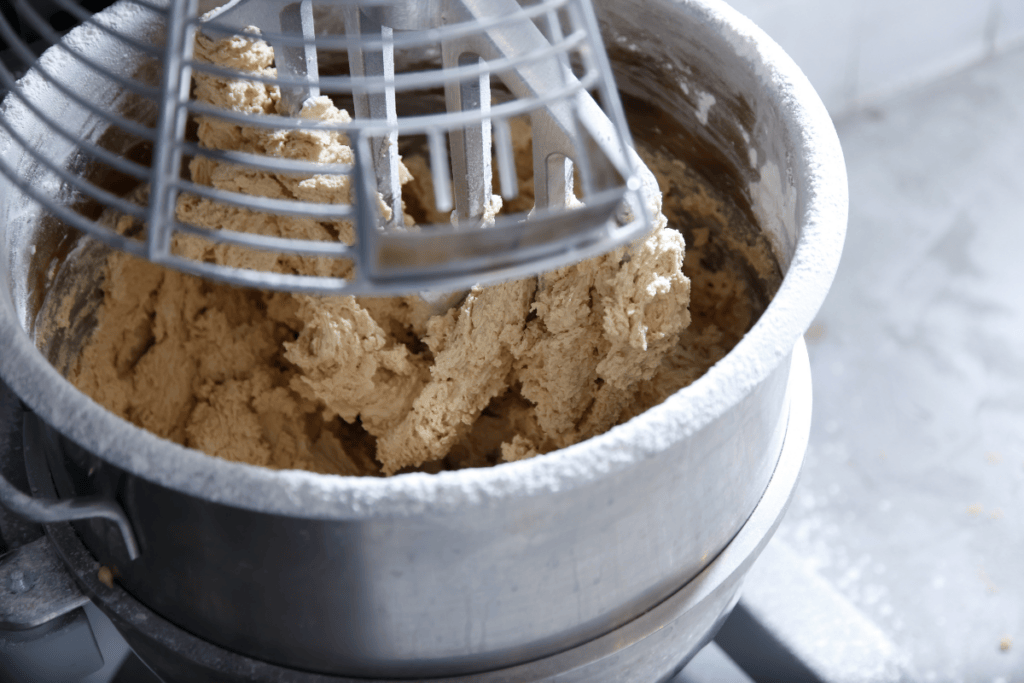
Unique Challenges of LOTO in Food Manufacturing
Lockout tagout is a safety precaution that is incorporated into a wide variety of industries and work environments. Here are some of the specific challenges that come with implementing it in the food manufacturing industry.
Frequent Maintenance and Cleaning:
- Explanation: Food manufacturing requires frequent maintenance and cleaning of equipment to prevent contamination and ensure consistent product quality.
- Challenges: The high frequency of maintenance activities can lead to complacency or shortcuts in following LOTO procedures, increasing the risk of accidents.
- Solution: Organizations must emphasize the importance of adhering to LOTO protocols during every maintenance task, regardless of frequency. Regular training and reminders can help reinforce the significance of these safety procedures.
Complex and Diverse Machinery:
- Explanation: The industry uses a wide range of machinery with varying energy sources, including electrical, mechanical, thermal, and hydraulic systems.
- Challenges: Identifying and isolating all energy sources for complex machinery can be challenging, particularly in older facilities with outdated equipment.
- Solution: A thorough assessment and documentation of all energy sources for each piece of equipment are essential. Detailed LOTO procedures must be developed for every machine, and employees should be trained to understand and implement these procedures accurately.
Hygiene and Sanitation Requirements:
- Explanation: Food manufacturers must maintain high hygiene standards, which often involves the use of water, chemicals, and other cleaning agents.
- Challenges: LOTO devices and procedures must be compatible with the sanitary requirements of the food industry. Traditional LOTO equipment may not be suitable for environments where contamination is a concern.
- Solution: Use LOTO devices made from materials that can withstand regular cleaning and exposure to food-safe chemicals. Additionally, LOTO procedures should include steps to ensure that the devices themselves do not introduce contaminants into the production process.
By understanding these challenges and making efforts to utilize solutions, companies can best practice lockout tagout and reap the benefits from it.
Lockout Tagout Best Practices in the Food Industry
Developing Equipment-Specific LOTO Procedures:
- Explanation: Each piece of equipment in a food manufacturing facility may have unique energy sources and shutdown requirements.
- Best Practice: Develop detailed, equipment-specific LOTO procedures that outline the exact steps for isolating and controlling hazardous energy. Include diagrams, pictures, and clear instructions to aid in understanding. This will serve as the foundation for a robust lockout tagout program.
Regular Training and Refresher Courses:
- Explanation: Ensuring that all employees are well-trained in LOTO procedures is crucial for maintaining a safe work environment.
- Best Practice: Conduct regular training sessions for all employees, including new hires, and offer refresher courses to reinforce the importance of LOTO. Training should cover both general LOTO principles and specific procedures for the equipment they work with. Have professionals perform the training and encourage them to use hands-on experience and visual aids to help trainees grasp concepts.
Conducting Periodic Inspections and Audits:
- Explanation: Regular inspections and audits help ensure that LOTO procedures are being followed correctly and remain effective.
- Best Practice: Implement a schedule for periodic inspections of lockout tagout practices and procedures. Identify any gaps or deviations and take corrective actions as needed. Audits should include reviewing LOTO records, inspecting devices, and observing procedures in practice. In the event that a LOTO violation is received, identify the root cause and address it to avoid repeat violations.
Leveraging Technology for Improved Compliance:
- Explanation: Modern technology can enhance the effectiveness and efficiency of LOTO procedures.
- Best Practice: Consider using software solutions and digital tools, such as QR codes, to streamline LOTO processes. These tools can provide instant access to lockout tagout procedures, automate documentation, and offer real-time monitoring of LOTO compliance.
FAQs for Lockout Tagout in the Food Manufacturing Industry
Here are some of the most common questions regarding lockout tagout and the food manufacturing industry.
- What kinds of equipment need lockout tagout in food manufacturing?
- Any form of machinery or equipment that could harm a worker through hazardous energy such as accidental machine start up should have lockout tagout procedures.
- What regulations apply to lockout tagout in the food industry?
- Key regulations for those dealing with lockout tagout in the food manufacturing industry include OSHA 29 CFR 1910.147, FDA 21 CFR part 110, ANSI Z244.1, and other local and international standards (such as ISO 45001).
- What is the purpose of lockout tagout?
- The main reason for performing lockout tagout procedures is to protect workers from hazardous energy. This is done by de-energizing and securing machinery during maintenance, inspections, or testing of equipment.
- What is the difference between lockout and tagout in manufacturing?
- Lockout and tagout are both essential steps for securing manufacturing machinery. The term “lockout” refers to the process of isolating a hazardous energy source and using a physical lock to secure it, while “tagout” involves attaching a warning tag to indicate that the equipment must not be operated.
- What kind of situations need lockout tagout?
- Lockout tagout should be used during any inspections, servicing, maintenance, testing, or repair work on machinery/equipment where unexpected energization could injure or harm workers.
- Why is performing lockout tagout procedures important?
- LOTO procedures are important because of the role they play in creating a safe work environment for employees. Not only this, but they help with improving compliance, avoiding costly repairs, minimizing risk, and more.
How Software can Simplify LOTO Procedures
Smart Safety Pro is a mobile software that aids in managing lockout tagout procedures, inspections, maintenance, and programs. Much like the regulations set forth by OSHA, our software is designed to be a tool to help keep your workplace safe.
Here are a few features and benefits that help with compliance:
- Since wifi isn’t required for our software to sync, users can complete reports on the go and get real time updates. This helps all management and team members better collaborate. They can know what tasks have been completed and what still needs to be done.
- Our software provides a centralized data management system that stores and organizes info. This feature can be particularly handy when collecting documents to show during audits and inspections.
- The system is highly customizable with the ability to build your own loto procedures in minutes. This way, as your company changes or regulations evolve, you can grow with them.
These are just a few reasons to integrate software into your lockout tagout operations. Click here to set up a demo and learn more about how Smart Safety Pro can help in your situation.
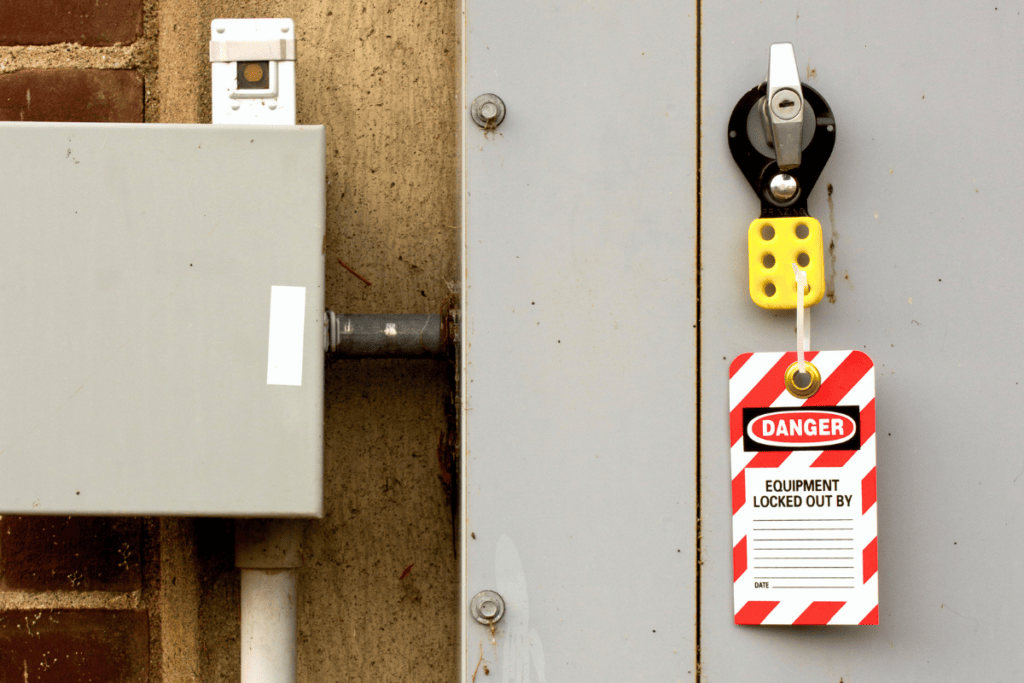
Conclusion
Lockout tagout procedures are essential in the food manufacturing industry. They serve as protection for workers from hazardous energy, help maintain food safety standards, and promote compliance. Because of these benefits, company owners and managers should familiarize themselves with regulations regarding lockout tagout. Some regulations to understand include those established by OSHA, the FDA, ANSI, and others. Knowing these standards, training on them, documenting work properly, and performing routine inspections are some of the best ways for organizations to benefit from LOTO procedures.
Though, it is good to note that the food manufacturing industry comes with unique challenges. Companies can offset these challenges by implementing lockout tagout best practices such as having equipment specific procedures, conducting inspections regularly, and utilizing software/technology.
Smart Safety Pro offers a top-tier mobile app for lockout tagout. SSP software can be used to simplify LOTO procedures and make compliance for food manufacturers that much easier! For more information about the software and how it can aid in running a LOTO program, request a demo here. Any and all efforts made by food processing institutions to perform lockout tagout can significantly reduce the risk of accidents and enhance overall safety in their facilities. Start today to improve safety at your workplace.